Basic Info | Food Safety | Slips | Shrinkage | Oven Safety | Absorption & Microware Safety | Deflocculation | Brown Stoneware Composition |
This page provides additional, more technical information about clays and related materials.
Slips
This discussion of slips pertains to ones for high fire clay bodies. Materials and considerations for terracotta are different (consult your instructor for details).
Clay is a fine-grained, natural soil material. The clays used for pottery typically also include other ingredients for performance and stability. Glaze is a vitreous mixture which bonds to the clay at high temperatures, forming a hard surface on the vessel. Between the realms of clay and glaze there is a continuum of mixtures that exhibit some properties of both to varying extents:
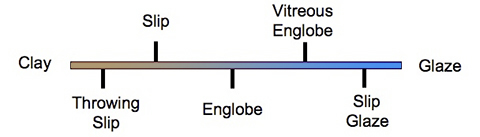
This spectrum offers a general way to describe these mixtures, but the terms and properties are by no means rigid or universally used.
Barringer, Studio Potter, 12/1995
Slips are mixtures of clay and water blended to a creamy consistency, possibly with a colorant added. They have to be used on wet or damp clay only; otherwise, they will crack as they dry and shrink. See also the information on deflocculation below.
Englobes are similar to slips, but they contain relatively less clay and also include fluxes and colorants to behave more like a glaze. Englobes can be used on bisque, and they will often fire to a matte finish.
Vitreous Englobes are englobes with a still higher proportion of glaze ingredients, intended for bisque application, and they may be used instead of a glaze to create an impermeable surface.
Slip Glazes are clays that will form a glaze at stoneware temperatures without any additional flux. These are useful in making once fire ware.
Terra Sigillata is a type of slip made from terracotta clay. It only contains clay, deflocculant and sometimes colorants. The sheen of terra sigillata results from its very fine particle size and from the physical polishing that potters perform after applying it.
Available Slips & Washes
At CAW, available slips for high fire clays are stored on top of the partition between the main area and the glazing area of the studio. When standing in the glaze area, facing the sliding glass door, available items are stored in these locations:
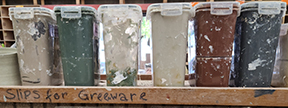
On the left: Slips for use on greenware are in taller containers.
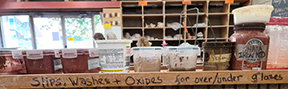
On the right: Slips, oxides and washes and other items for use on bisque, usually in shorter containers.
Oxides and washes are mixtures of ceramic colorants—typically, metal oxides—and water. They are very thin and watery since they contain little to no clay, fluxes, or other minerals.
A CAW standard offering is Red Iron Oxide, which consists of Iron Oxide mixed with water. This mixture is strong enough to darken an unglazed stoneware surface during firing. Sometimes oxides are used to sign a pot after bisque, in lieu of incising the greenware.
CAW Brown Stoneware Composition:
22% | Goldart Stoneware Clay |
22% | Hawthorne Fireclay |
22% | AP Green Fireclay |
7.5% | Tennessee #9 Ball Clay |
7.5% | C & C Ball Clay |
7.5% | Redart Earthenware Clay |
7.5% | Fine Grog |
4.0% | Custer Feldspar |
Shrinkage
Basic information about calculating shrinkage is available here. This section describes the phenomenon in more detail.
From the time you take it out of the barrel or other container, clay shrinks. It shrinks more-or-less continuously until it reaches its final state after glaze firing. Ideally, clay shrinks slowly, evenly and uniformly. However, many factors can interfere, resulting in a product that is less than ideal. For example, if clay is dried too quickly, it is more likely that some parts of the clay will dry faster than others, resulting in internal stresses and possibly cracking.
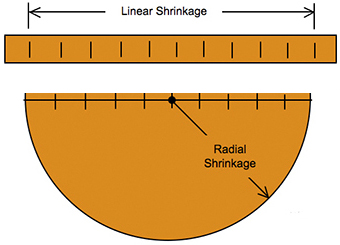
Clay does not shrink uniformly. For example, its shrinkage rates will vary for linear shrinking and radial shrinking on a diameter. For example, test performed several years ago on the brown stoneware clay then in use found a difference on 1.25%: small but significant (radial shrinkage was greater than linear shrinkage).
Shrinkage Rates for Different Clays
**Manufacturer’s rates for available clays.**
You can determine the shrinkage rate for a clay you are using by making a test strip, measuring it in the wet state, and then firing it as you plan to fire your desired pieces. One common way is to press a plastic ruler with raised lettering into the wet clay, creating a built-in measuring scale. At each point in the process, you can measure the shrinkage but also see it visually.
When complete, you can use this tool to “measure” a fully fired piece and thereby determine how large a wet piece would need to be in order to have the same final size. For example, if a piece lines up with the number 5 mark on the fired “ruler”, then another piece would need to be 5 inches to end up the same size as the one you are measuring (which is, of course, smaller than 5″ in reality).
Oven Safety
For a ceramic food container to be oven safe, it should withstand being taken from a freezer and placed into a preheated oven. Since the temperature of a standard household freezer is 0°F, and baking temperatures are typically 375°F or less, a thermal shock test involving a rapid 400 degree temperature change would adequately demonstrate oven safety.
A studio test was conducted in which 25 test cups, each glazed with one of the studio glazes, were preheated to 500°F in an oven, and then immediately quenched in a room temperature water bath (70°F). This cycle was repeated 3 times. None of the cups showed any sign of cracking or crazing. The test was repeated with the same cups one year later, and again there were no signs of cracking or crazing in any of the samples.
Experimental Details: Nearly identical test samples were made from a hollow tube of studio stoneware pressed through the Brent Extruder. The tube was cut up into short equal lengths, approximately 2.375 inches tall, with each piece then scored and joined to a flat slab base. This created a 90° (i.e.,: worst-case) platelet misalignment at the extrusion-to-slab joint.
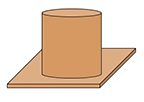
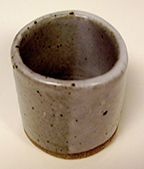
The samples were then bisque fired and glazed along a vertical axis with one coat on the left, and two coats on the right. This sample was glazed with gloss white.
Absorption Tests: Microwave Safety
Vitrification tests are done to verify that studio clays and firing processes result in a fully matured product. For stoneware, full maturity is reached when the ware absorbs no more than 2% – 5% of moisture by weight after glaze firing. Absorption is the primary determining factor for microwave safety. If the ware absorbs too much water, it may crack or even explode from the pressure of internal steam during microwave cooking.
To check CAW’s clay and process, four unglazed tiles were made from our latest brown stoneware blend, placed at extreme locations in the Phoenix kiln, and glaze fired on 12/10/10. They were immediately weighed after the kiln cooled, then submerged in water for 24 hours at room temperature. Afterwards, surface water was removed, and the tiles were weighed again.
Absorption was determined using the following relationship. Results are presented in the following table.

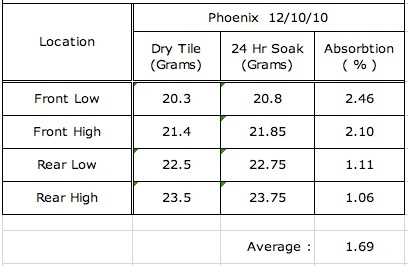
Based on the table, our average absorption for the current studio stoneware is 1.69%, with the highest measurement being about 2.5%, indicating that all samples were well within the recommended limit.
For reference, photographs were taken of the cone packs for the 12/10/10 Phoenix firing. Note that cone 10 in the upper pack tipped to about 2 o’clock, while cone 10 was fully down in the lower pack. Interestingly, there appears to be a stronger correlation between readings in the front and back of the kiln, rather than between the top and bottom.
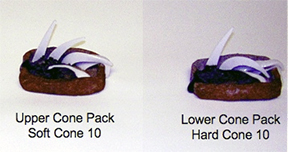